Industry
How to be More Resilient, Make Better Decisions Faster, and Achieve Uninterrupted Mission Readiness
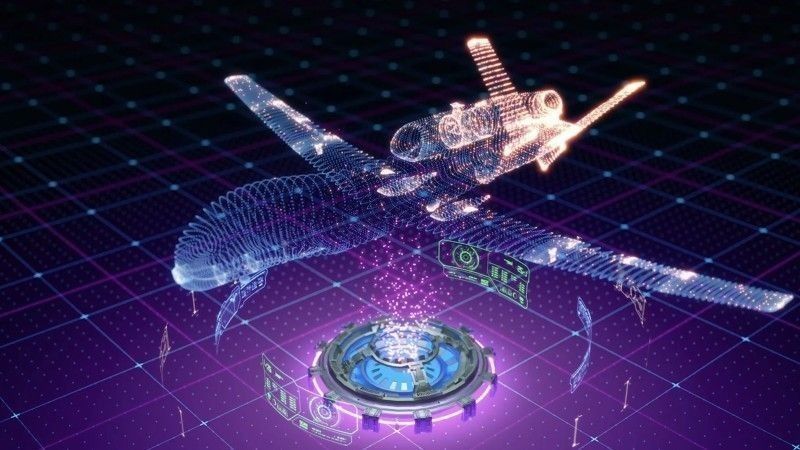
In today’s contested environments, military leaders operate under constant threat of attack across all operating domains — land, sea, air, space and cyberspace. Future mission readiness will require secure support for smaller „distributed” operating bases with real-time logistics tools to plan, forecast and deliver critical assets where and when they are needed.
A sponsored article, publishing partner Northrop Grumman
Data-enabled analytics are the key to managing risk and meeting mission requirements. Using "predictive analytics" that identify the likelihood of future outcomes and "prescriptive analytics" that recommend the best courses of action, leaders can make better decisions faster, proactively identify trends and address vulnerabilities.
Northrop Grumman pioneers innovative digital technologies to help customers achieve higher states of readiness at a lower cost.
A Digital Difference
A "digital environment" uses data analytics to predict timing, cost and impact of future sustainment activities along with real-time visibility into current maintenance work, including parts and personnel availability. Predictive simulations provide forecasts of sustainment costs and condition-based maintenance. Supply chain risks are managed with the digital environment's "autonomic supply" capability that lowers costs and provides parts at the right time and place.
A digital environment with powerful analytics makes it possible to continuously assess and evaluate the wear and tear on a given weapon system (for example, an aircraft and its components) to predict which elements will require servicing or replacement and plan for those activities well in advance. There is no need for time-consuming equipment decommissioning and unpredictable Program Depot Maintenance (PDM) that requires disassembling an aircraft into individual parts.
Real-time visibility of part inventories and prescriptive analytics transform control of the supply chain, which dramatically reduces lead times and lowers costs to achieve decision advantage and keep weapons systems operationally ready anytime, anywhere.
A Digital Twin
An important benefit of a digital environment is use of the "digital twin" coupled with 3D scanning to capture defect conditions and enable creation of very accurate "as-maintained" models with precise definition of features and performance. These models are then used to analyze and test everything from the risks associated with equipment wear to options for modernization. Digital models can be created for platforms, mission subsystems, support equipment, and individual component assemblies.
Digital twins are useful for older generation aircraft, which can require modification, replacement of obsolete elements and modernization to keep them relevant and at optimal readiness. With a digital twin, if a particular component is no longer available, a replacement can be designed and tested on a virtual model before any equipment is manufactured or moved in the real world. A digital twin can be used to test, modify and simulate performance over time or within specific conditions. All the data gathered can be analyzed to further inform future decisions about sustainment and modernization. By using virtual simulation and real-time data, a digital twin rapidly evaluates system performance in ever-changing environments.
Sustainment and Persistent Modernization
To keep up with emerging threats, defense systems require sustainment and "persistent modernization," stemming from an understanding that technology developments are only accelerating, never stopping. Careful maintenance and ongoing upgrades are especially important as legacy platforms age. Innovative digital technologies can significantly improve availability, performance and reliability to support mission readiness.
For example, even if a legacy aircraft can perform transport tasks for an extended time, it may be equipped with avionics equipment that differs from modern standards, which hinders training and maintenance. A uniform, digital standard will significantly simplify training and maintenance. Instead of many avionics variations with different standards – some of which may no longer be produced – standard modern components are used and can be easily improved or replaced if necessary.
Northrop Grumman partners with our customers to support "digitalization" and modernization throughout the entire program lifecycle to develop, deploy and sustain capabilities faster than ever before on a wide range of manned and unmanned platforms.
Partnering for Success in the Digital World
In the face of new and existing global threats, Northrop Grumman is a trusted provider of services and products related to the maintenance and modernization of military equipment across numerous platforms and mission payloads (platform and payload agnostic). Modern digital technologies are integrated to improve combat readiness and plan for repair and modernization, which translates into lower costs for our customers.
Secure, networked infrastructures using digital tools and open architectures are critical for global connectivity and collaboration. When they are in place, workers can be trained remotely using virtual reality (VR), augmented reality (AR) and mixed reality (MR) classrooms to help mechanics familiarize themselves with equipment even if it is not physically available to them.
Whether supporting the entire lifecycle of a system or for specialized solutions such as the design and delivery of equipment for a given platform, Northrop Grumman works in partnership with local industry. Implementation of digital solutions will bring new levels of potential to existing platforms and open doors to new technologies as they become available.
A sponsored article, publishing partner Northrop Grumman