Baobab – Evolution of the Polish Scattered Mine Delivery System
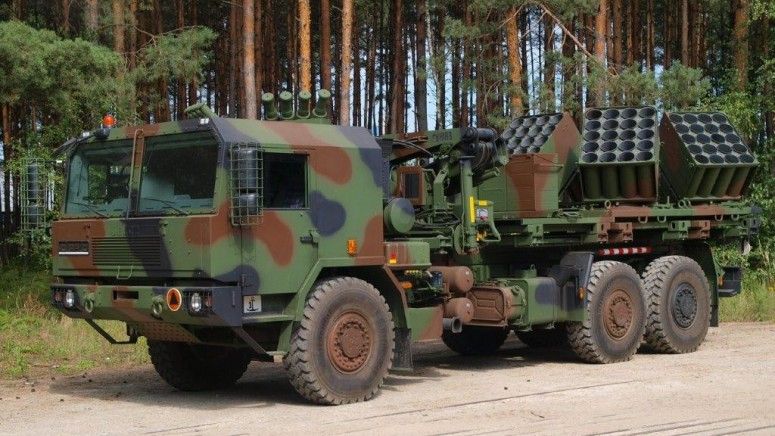
HSW S.A., acting as the leader of the consortium working on the Baobab-K programme, assures that work on the Baobab-K scattered mine delivery system is progressing in line with the adopted schedule. The original plan was created as a part of the relevant agreement signed on 28th December 2018. Noteworthy, this is the fourth attempt that the military is making to acquire a cost-effective, efficient and simple anti-tank asset.
The abbreviation PMN - Scattered Minelaying Platform - was the original name of the vehicle. Currently, it is known as the Scattered Minelaying Vehicle, under the very same, Polish acronym, just referring to different terms. It is being developed, apart from HSW S.A., the consortium leader, by BZE BELMA S.A. (MN-123 anti-tank mines, mine cassettes, and launchers supplier), Jelcz S.A. (supplier of military high-mobility trucks), and, finally, the effort also involves the Military Institute of Engineering Technology. The R&D processes that had been previously initiated, carried out since 2014, were subject to cancellations justified by a myriad of reasons, including a mismatch between the financial requirements of the Supplier and financial ability of the Ordering Party. Ultimately, the design and development stage of the development project had a price tag agreed at the level of 19.9 million zlotys. This concerned the prototype of the vehicle and relevant documentation.
For the sake of clarity, one should note the following: HSW has developed several scattered mine delivery systems compatible with the MN-123 anti-tank mines, and the company has gathered a lot of experience dating back to the 1990s. The expertise refers both to the technology, as well as to the organizational processes - and this know-how is indispensable when working within the framework of a consortium gathering several entities that conduct their activities in several different defence industry domains. The undertaken effort also involved military research institutes.
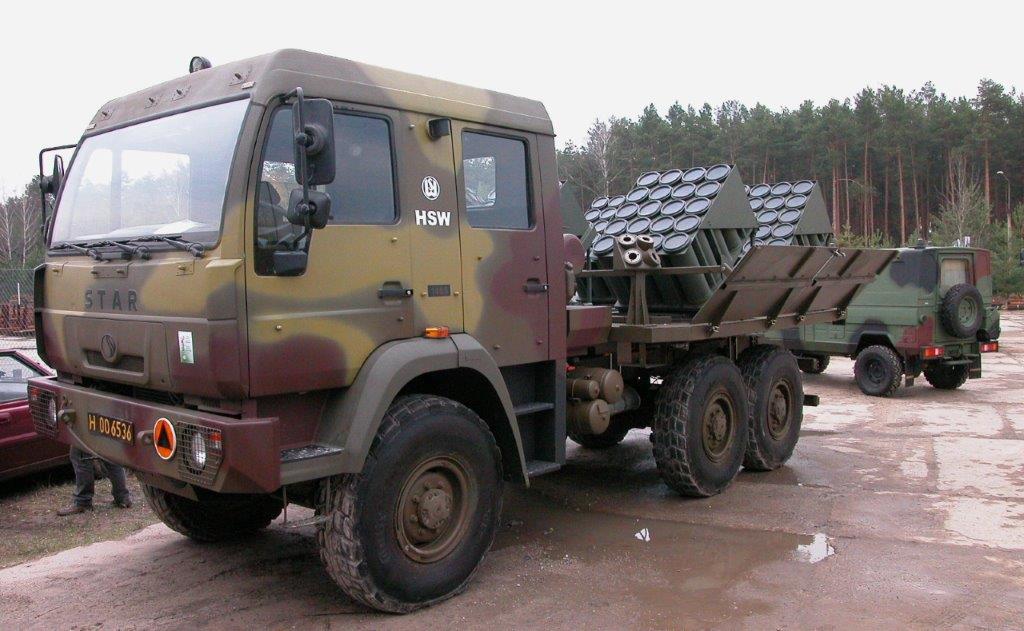
The first attempts made to create a scattered mine delivery system using four MN-123 mine launcher blocks, integrated on the Star 1466 platform, turned out to be a dead end. However, these attempts made it possible to indicate the potential directions in which platforms of this class could be developed. They also made it possible to define the principles for operational use. Fiasco had some well-known reasons that had nothing to do with HSW. The problems emerged at the car factory in Starachowice that was acting as the primary supplier of the off-road heavy-duty vehicles used as the base platform. For the very same reasons, HSW resigned from developing an upgrade of the BM-21 rocket launch system, using the very same carrier platform. Change of the carrier platform led to an evolution of the programme that resulted in the creation of the WR-40 Langusta solution. The system in question uses a special-purpose vehicle designed, from a scratch, to be used in military applications. The 3-axle Jelcz vehicle is far more advanced and offers much greater capabilities. The truck in question has a large, armoured cabin that can accommodate the whole launcher crew.
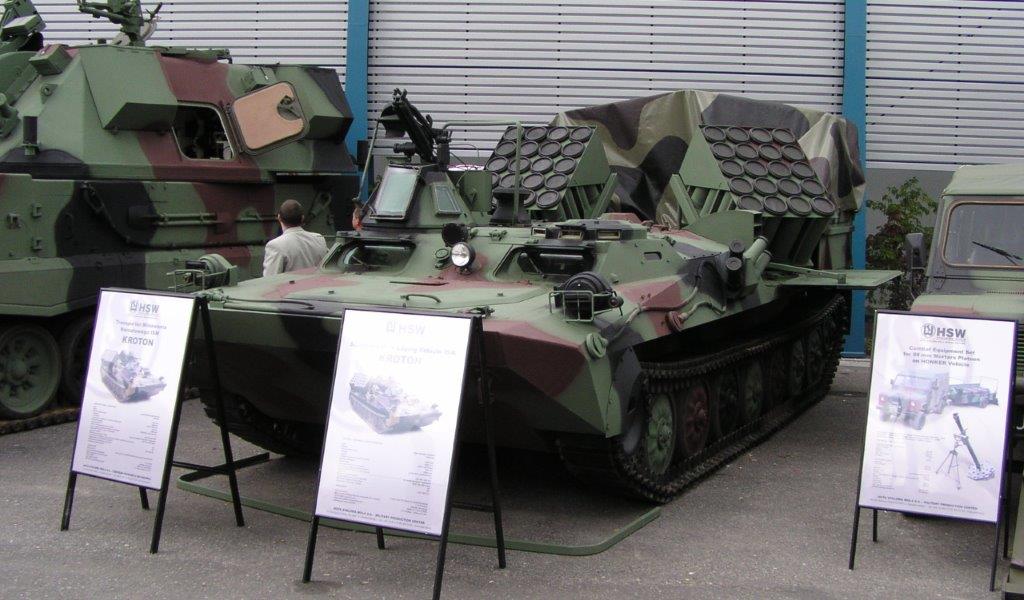
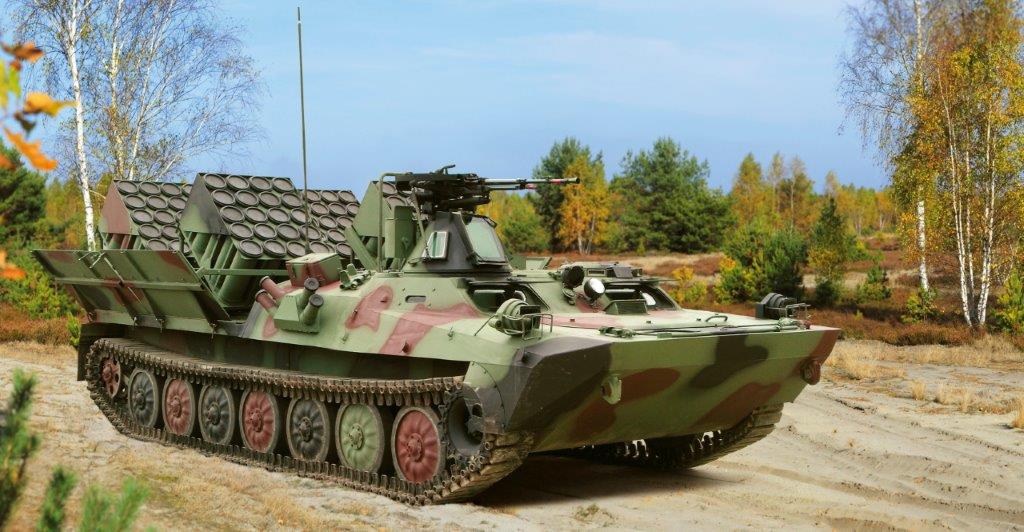
The experience gathered when working on the scattered mine-delivery system, using the Star 1466 vehicle, was used by HSW to create a 16-tonne TMN (Transporter Minowania Narzutowego - Scattered Mine Delivery Carrier) Kroton platform. This vehicle used the modified amphibious MT-LB vehicle as its base. Among other modifications, it had one additional pair of wheels added, and it was known under the MT-LBu designation. Kroton featured four mine delivery blocks containing, in total, 400 removal-proof shaped-charge MN-123 anti-tank mines. They could be detonated immediately, or with a delay.
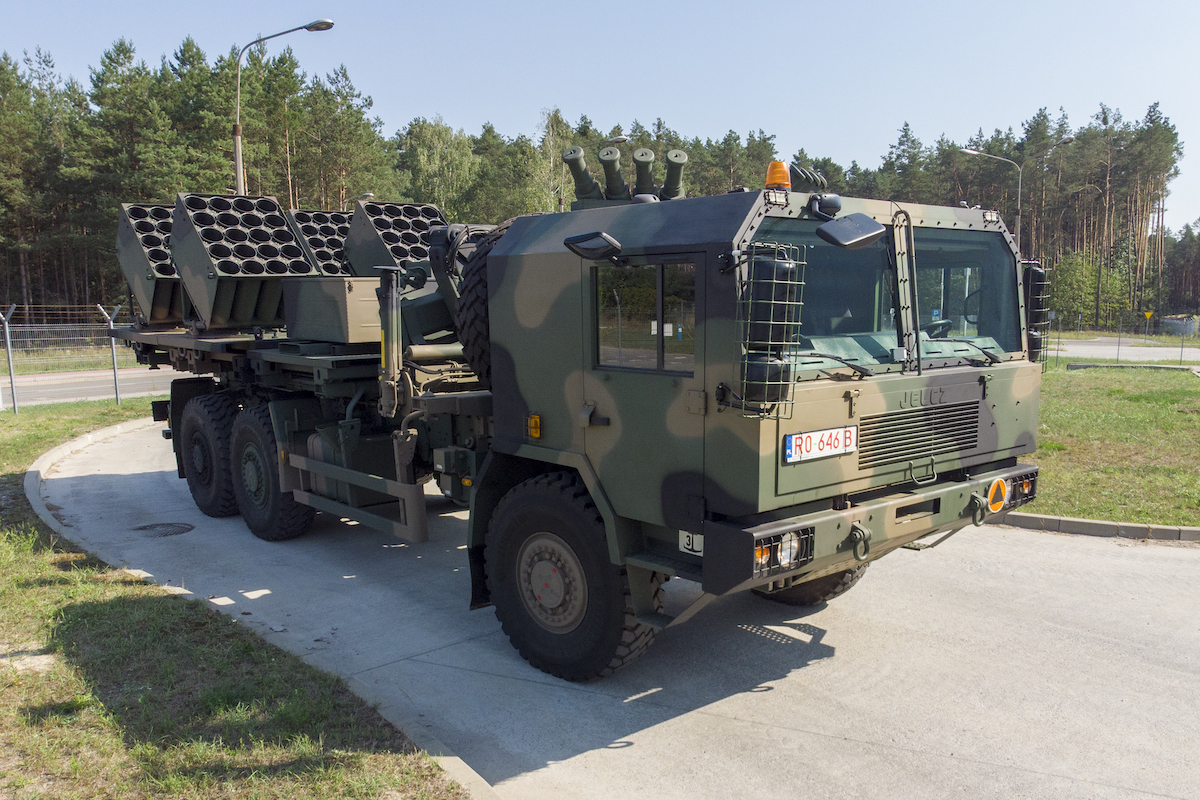
The launcher systems were set up manually. Tech support is required to replenish the effectors (mine “cassettes” or “cassette” blocks). Nonetheless, Kroton was a qualitative leap forward in the engineering component, raising the operational effectiveness in the area of creating minefields that would form a defensive barrier against the attacking armour. TMN ISM Kroton, with a crew of two, can create a minefield that is 30 to 90 meters wide, with a length of 600 meters. A minefield like this can stop the enemy armour, slow it down or force it to change the direction of movement - to bypass the obstacle. The enemy may remain stuck until the mine-field self-destructs. Assets as such are very valuable in area denial operations that restrict access to water obstacle crossing areas, narrow passes between natural obstacles (such as levees), bridge approaches, and so on. Minefields created by these platforms may also delay gathering of the armoured units, forcing them to carry out specific maneuvers and allowing their anti-tank assets to gain a tactical advantage in neutralizing the emerging threat.
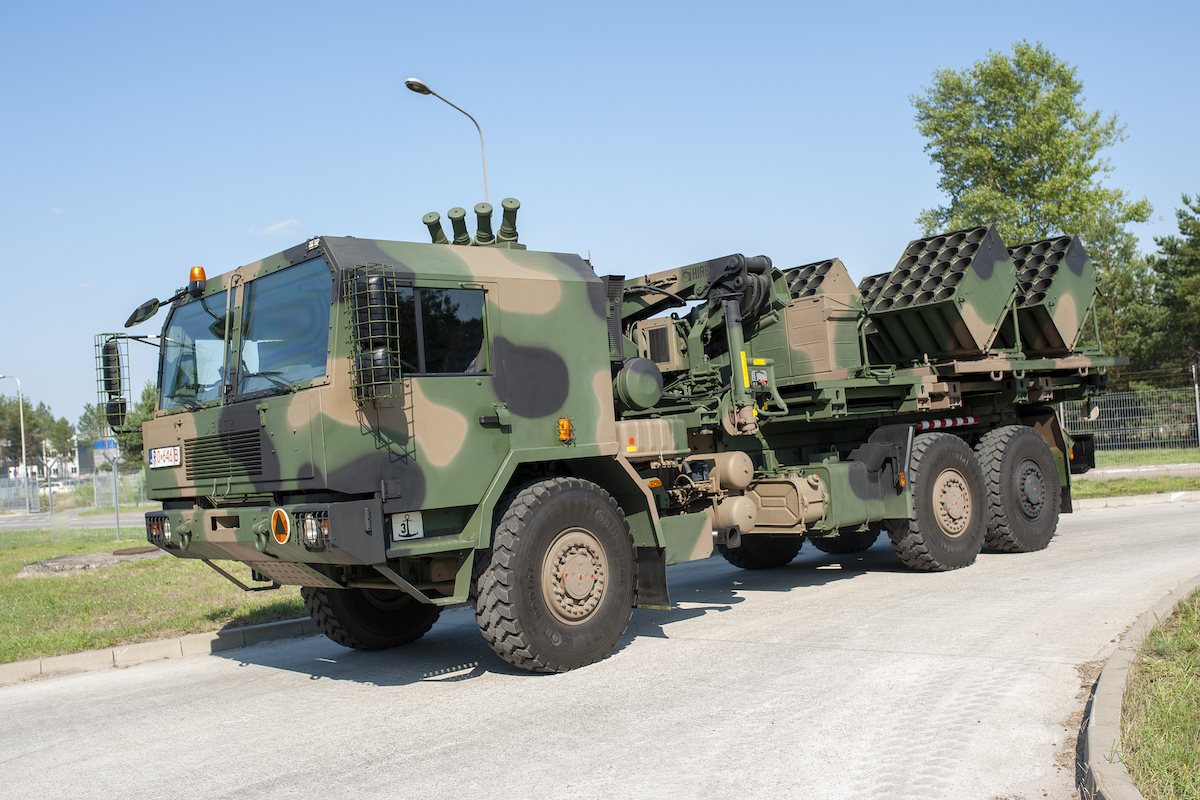
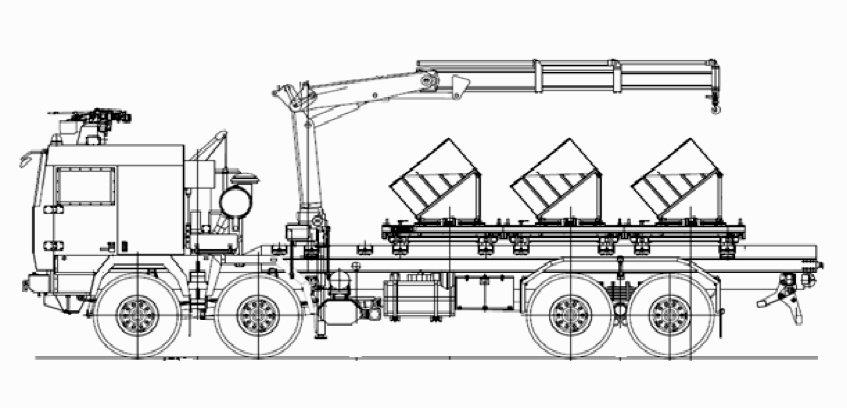
The Polish military has acquired a minor quantity of these systems back in 2005. The platform has seen some successful use. Periodic maintenance is carried out at HSW.
The experience gathered during the Kroton 2.0 project, as well as the interest signaled by the Polish MoD, with regards to a wheeled scattered mine-delivery system, altogether led to the emergence of a new solution. Notably, the “Kroton” name had been used back in the 1980s, with regards to another, the legacy project concluded by the Gliwice-based facility, aimed at developing a tracked SPG-1 platform scattered mine delivery system with eight mine launching cassettes. Baobab system developed by HSW and officially rolled out during the MSPO 2007 exhibition was the first technology demonstrator that fused six launcher blocks (120 cassettes with 600 MN-123 mines in total) with a 3-axle Jelcz P662D43 platform. The chassis also featured HIAB crane, offering an autonomy boost for the platform when recovering its readiness. The evolution progressed, as the project was moving forward when another wheeled PMN Baobab prototype was created. It also uses a 3-axle Jelcz P662.34G34 vehicle with a spacious, armoured cabin. This variant of the vehicle uses four launcher blocks.
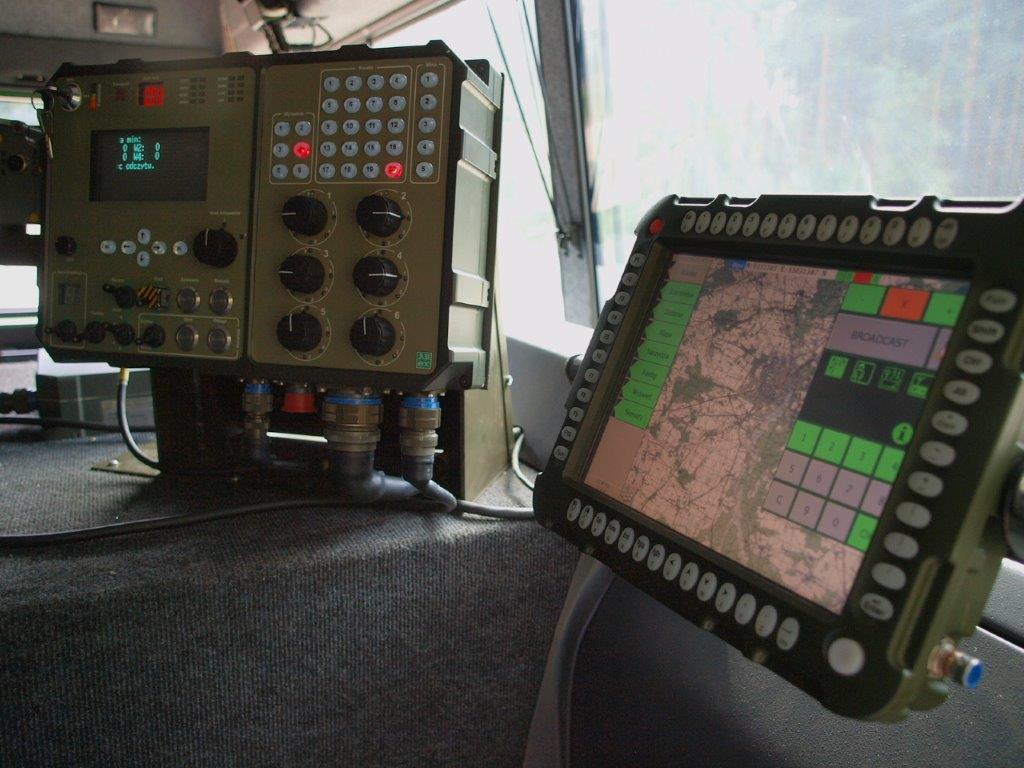
Creating a minefield in 20 minutes, as required, is also supported by modern equipment automating the mining process and the data exchange, necessary to define the minefield parameters. Baobab, in its current form, features an onboard computer, visualization terminal displaying a digital map, GPS, odometer, and VHF radio. Furthermore, the vehicle uses the FONET intercom system. A separate control panel has been provided to control the 81 mm smoke grenades launcher system used for self-protection. The vehicle is fitted with a HIAB loading system as well. The launchers with mine cassettes need to be put in combat setting by hand. However, this requires much less force than in the case of the Kroton platform. The vehicle carrying full mine launchers on its back weighs 21 tonnes.
The newly defined requirements also indicate a need to introduce relevant design changes. This also means that the weight of the platform, with launchers, would be higher. However, it would also be fitted with several systems automating the launcher settings. Above all, however, the new platform would also feature a new crew compartment with a remotely controlled gun system on its top - the cabin roof is to be able to accommodate the extra weight. The system as such would boost the vehicle’s self-defence capabilities. The cabin used so far only offered the ability to mount a GPMG mount on its top. Most probably it would not be rigid enough to accommodate a heavy module with an ammunition storage unit. The cabin had to be redesigned to make it possible for the commander to control the machine gun station. The commander also assumes the role of the mining system operator. The mining system panel would be accompanied by the gun module panel which could lead to work overload. This led to a situation in which a necessity emerged to design a new cabin layout. This, in turn, would require a more durable carrier platform.
Thus it would also be required to put the new cabin design through its paces throughout a complete test cycle, including ballistic protection levels testing (with live-fire tests included as well). This translated into a practical necessity to begin most of the design effort from scratch. And this would mean that more time would be required, along with more funds, corresponding with the scale of the task.
So how the final form of the Baobab system is doing? The system is going to become a component with its operational meaning similar to the one associated with the best known scattered mine delivery solutions around the world: UMZ, Volcano, Shielder or Minotaur.
Baobab-K programme is progressing in line with the adopted plan and schedule. There are no potential obstacles on our side. We, as the Contractor, will deliver on agreed deadline.
After one year that passed from the agreement conclusion, we know that we will witness a certain departure from the original assumptions, in case of the new Baobab-K platform. Automated launcher control system requirement remains in place, as defined by the Ordering Party. To deploy the launchers in combat, hydraulics are used. Meanwhile, rotation is to be ensured by a system of electric motors. Parameters of the system need to be brought up here. Each of the launcher blocks consists of 20 barrels containing cassettes with 5 mines in each cassette. And a single block weighs 880 kilograms when loaded. “Dry” weight is 360 kilograms. This means that motors need to be efficient enough, with the platform mount being durable and rigid enough. It is also required to provide the system elements (motors, cables and so on) with proper protection measures (armour). Contrary to what may seem, designing a mechanical system as such for launcher block control is far from simple. The load imposed on the system’s critical points by the launcher blocks needs to be taken into account, along with G-forces associated with the dynamic offroad movement of the vehicle.
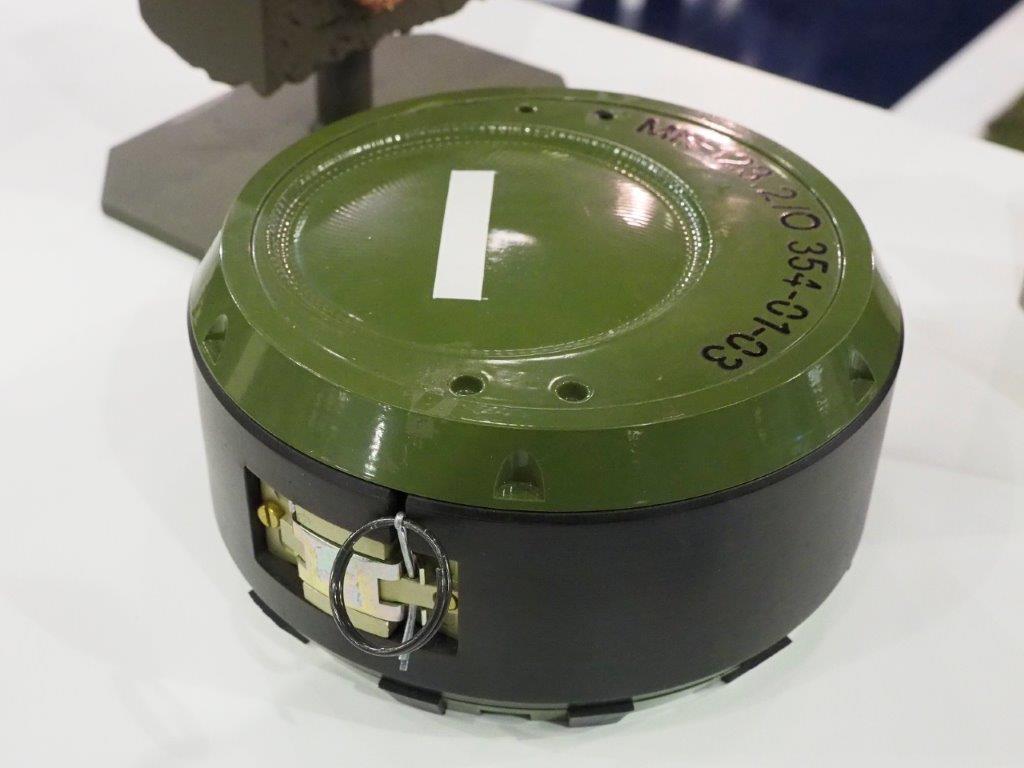
As the technical requirements were defined for the minelaying system, development of an even more advanced control system was envisaged within the Baobab-K project. The Baobab system presented many times already had the ability to create minefields manually or automatically. The commander’s terminal served as a visualization terminal that also could present the mission report on a digital map. Reports as such could be sent up the chain of command. The new Baobab-K system is to additionally allow for direct and automatic command input provided from the higher levels of the command chain when it comes to the mine delivery process. The design is ahead of its time, as no higher levels of command chain exist within the scattered mine delivery system used by the engineering component. If a relevant command chain is created then Baobab-K would be easily integrated within it, being already equipped with all of the required elements and software. HSW already has elements of that system ready for being installed on the prototype. These elements have been developed by AREX and WB Electronics.
The necessity to install the ZSMU (Remote Control Armament Module) unit on top of the vehicle also had a relevant impact on the agreement. As the ZSMU was still being developed when the agreement was signed, it was assumed that the inclusion of the module in the project could pose a delayed deadline. Ultimately then, even though ZSMU has been a part of the Baobab-K requirements, it is not a part of the contract. This made it possible to use the existing cabin design for the prototype, already tested and manufactured for the ammunition carrier, with an open gun station on the top. This, on the other hand, shortens the time required to develop the final prototype, also introducing savings. However, as the platform weighs more (which is dictated by automation and launcher setting motors) using a higher load capacity platform was unavoidable - the new vehicle uses a 4-axle layout. Creating a platform of this class for the Baobab-K system is perfectly possible for the Jelcz company. Similar vehicles have been already developed for the WA and AWA ammunition carriers. Should this solution be adopted, the launchers’ platform can be quickly dismantled and replaced by a new one. The truck itself may be employed for other purposes as well.
This solution arranges the situation and makes it possible for the work to progress fluently. HSW S.A. declares that model tests of the Baobab-K system could begin during the 2020 Q1. The tests will be focused on the new functionalities, design points and systems of the platform first. Only after these tests come to an end, a prototype would be created. The prototype is the product that is to undergo the actual qualification test programme. Procedures as such have been defined by the agreement concluded in December 2018.
Should any problems emerge, that the consortium will have no control over (for instance, related to the evolution of requirements), then 2021 is the definitive deadline for completion of work related to the acquisition of a simple, cheap, effective, yet technologically advanced system. The purpose and potential offered by that solution would equalize the disproportion of capabilities in the armour domain - between the Polish military and the potential adversary.
Baobab-K will use MN-123 anti-tank EFP-shaped-charge mines weighing 3.7 kilograms each. They feature a magnetic fuse and self-destruction/self-neutralization systems. The 60 mm RHA penetration capability is enough to go through the bottom section of the hull of the armoured vehicles, including most of the contemporary main battle tanks. Width of the minefield that is created remotely can be adjusted - it can range from 30 to 180 meters. Minefields can be set up remotely - on the opposite bank of the river for instance, without any need to send troops there. The density of the minefield can also be adjusted. It is also assumed that Baobab-K would offer the greatest range of mine delivery in its class. Minefield width of 180 meters with a length of 1 kilometer is achievable, with 600 mines involved. Creating a barrier as such would not take longer than 3 minutes.
So far the quantitative shape of the Baobab-K procurement is unknown. There are no premises to estimate the date on which work would begin aimed at starting the process through which solutions of the wheeled platform would be subject to a transfer to a tracked vehicle (Baobab-G system that could support the heavy brigades). K9PL/PK9 (Krab sph) or MPG platforms could be used here. The same applies to the MPG platform with a hydropneumatic suspension system. This solution was presented during the MSPO 2019 event. Soon, Borsuk IFV chassis will also become available, as a potential carrier.
The Polish military is expecting the new mine delivery system, and these expectations are high. The demand also inspired a reaction on the part of the BELMA company, manufacturer of the MN-123 mines. The company also presented a mini-Baobab system using a single launcher block (20 barrels) on the light Arlan offroad vehicle. It was premiered during the MSPO 2019 exhibition. Arlan is a derivative of the South African Maurader vehicle, developed with the Kazakh military in mind. A concept as such is a response to growing demand associated with the use of the scattered mine delivery system - in a hot climate for instance. MN-123 mine systems export potential and Baobab-K-based solutions are both a subject of discussions at HSW as well. However, potential export contracts are impossible to discuss. We need to wait until the system is introduced in the Polish military. Many signs suggest that the program is headed towards success, despite the term of turbulent vehicle configuration arrangements. This scenario forecast is justified by the knowledge of the progress made during a period of little over a year from the conclusion of the agreement.
Jerzy Reszczyński
All images by J. Reszczyński, unless otherwise specified